Strategic Partnerships
Integrating World-Class Products, Software, and Technology for Superior Solutions.
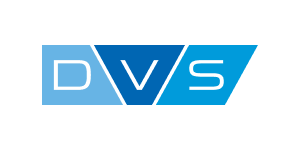
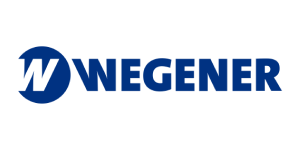
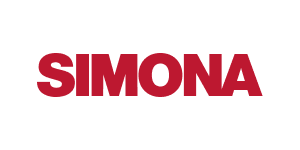
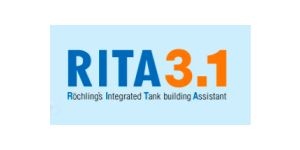
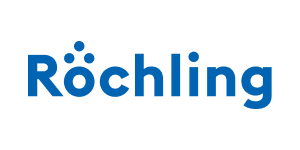
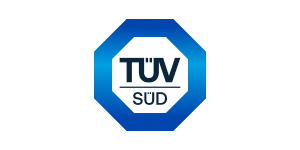
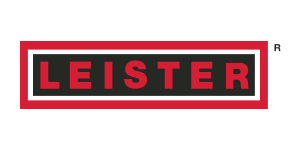
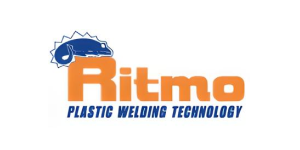
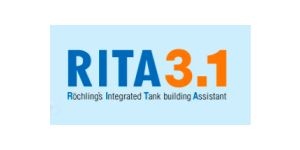
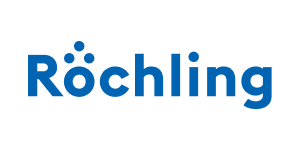
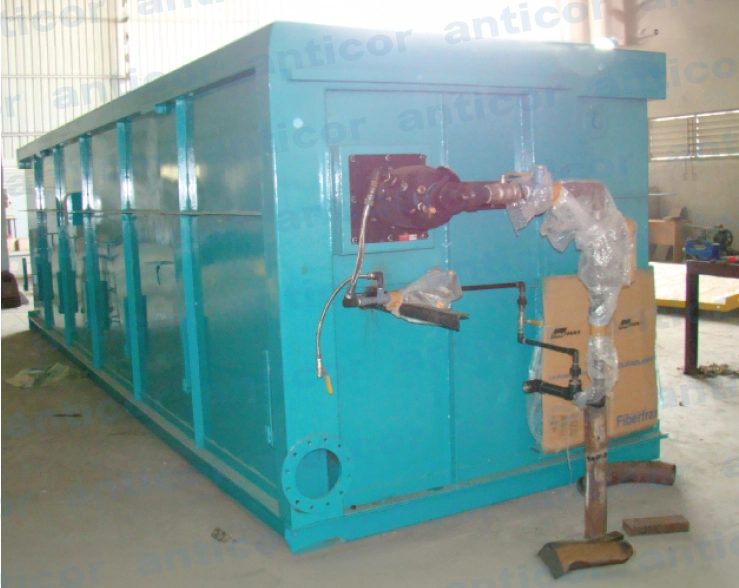
Hot Dip Galvanizing Plant
Arvind Anticor is amongst the leading hot dip galvanizing plant manufacturers in India as our product designs are most advanced and efficient. The product designs are fuel efficient, with a practical layout, easy to maintain, productive and furnished with innovative material handling systems. All our projects are managed by a dedicated project team for smooth implementation of each project.
The top management employees have years of experience in the hot dip galvanizing industry that includes design and installation of the galvanizing plant, operations management and proven performance record. We implement the entire project right from the beginning to detailed designing and installation.
Our galvanizing furnaces are manufactured using the finest quality of stainless steel acquired from well-known vendors in the industry. Our galvanizing furnaces are known for their qualities such as strength, high durability and corrosion resistance. The furnaces are frequently used to galvanize small components like fasteners and auto parts and large parts like poles, pipes and pillars. Our high-quality products have made us one of the well-known hot dip galvanizing plant suppliers in India.
Every project supply includes plant layout and design, supply and installation of galvanizing furnace, dryer, state of the art pre-treatment tanks, fume extraction systems for acid and zinc, flux heating system, flux recovery system, post treatment tanks and project management of third-party equipment.
Our team is able to successfully cope with the ever-changing customer needs of the galvanizing industry, operating processes and equipment supply. Our constant innovation in the products has helped us become one of the most well-known hot dip galvanizing kettle manufacturers.
Our range of products including scaffolding galvanizing plant and tube pipe galvanizing plant, can be used across various industry verticals as well as in foundry and mini steel plants for various processes such as calculation, ageing, homogenizing, baking and heat treatment.
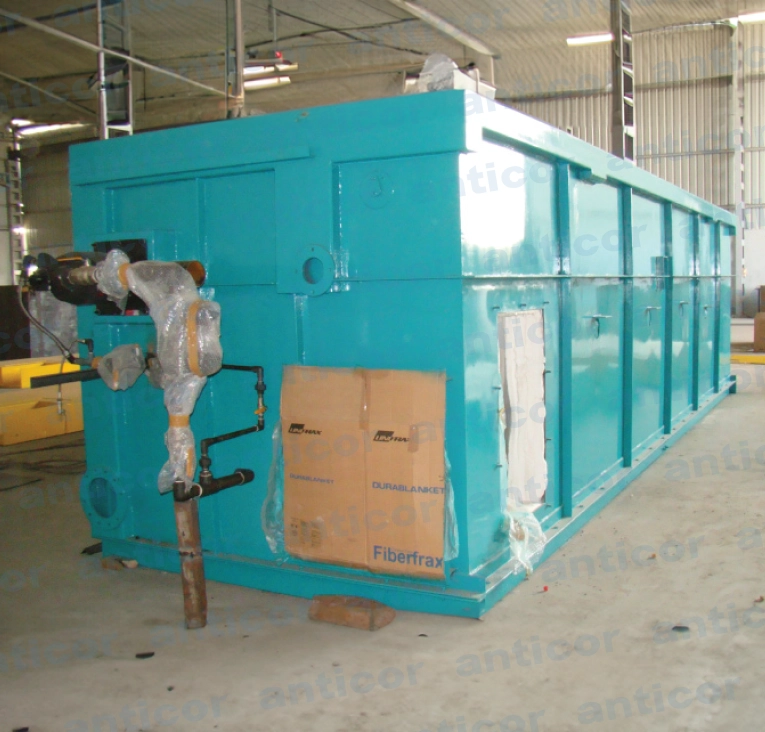
Specifications
- Project management and Engineering
- Feasibility Study Capital Expenditure and Justification
- Process Designing and Engineering
- Plant Layouts and Designing
- Finalize technical Specifications
- Design and Supply of Quality Equipment
- Construction, Supervision and Management
- Pollution Control Equipment
- Health and Safety Measurement
- Commissioning and Start-up
Why Choose Galvanizing Plant?
Exploring Benefits, Features and Industry Uses
- Low maintenance
- Used in various industrial applications
- Sturdy construction
- Galvanizing Kettles
- Pipe Galvanizing
- Flux Regeneration Systems
- White Fume and Splash Control System
- Pre & Post Treatment Plant
- Flux heating system
- Flux regeneration & filtration plant (frs)
- Work jigs, drosser, kettle cover, skimmer & ash buckets jigging & unjigging stations
- Plant layout, design & Trunkey project work
- Fully automatic galvanizing plant equipment pulse-fired.
- High velocity, dual fuel furnaces re-circulating hot air dryer, waste heat recovery system polypropylene pre-post treatment tanks
- Chemical Industry
- Water and wastewater treatment
- Agriculture
- Pharmaceuticals
- Power and Energy
- Automotive Industry
Gallery of Hot Dip Galvanizing Plant
Discover Comprehensive Turnkey Galvanizing Solutions Through Our Showcase
Any Questions ? We Got You.
Typically, ferrous metals like steel and iron are galvanized. Metals must be chemically clean and free from impurities to ensure proper adhesion of the zinc coating.
The lifespan depends on the environment:
- Mild environments: Up to 75+ years.
- Industrial or coastal environments: 20–50 years.
The coating’s thickness and exposure conditions play a significant role in its longevity.
The thickness typically ranges from 50 to 150 microns, depending on the material’s size, shape, and immersion time in molten zinc.
Yes, galvanized steel can be painted or powder-coated for additional protection or aesthetic purposes. This combination is known as a duplex system and enhances the lifespan of the coating.
Yes, the zinc coating acts as a barrier to moisture and oxygen, preventing rust. Additionally, it offers sacrificial protection, meaning the zinc corrodes instead of the base metal.
Inspection methods include:
- Visual examination for uniformity and coverage.
- Thickness measurement using a magnetic gauge.
- Adhesion tests to ensure proper bonding.
Related Blogs
Let’s Connect
Contact Us
We are live 24/7 and reply within 48 hours.
Get in Touch
-
-
-
Address
Survey No.584/1+2 – C,Nr. Akshar Industrial Estate Mahemdabad Highway Road,Vatva Ahmedabad-382445, Gujarat, India.