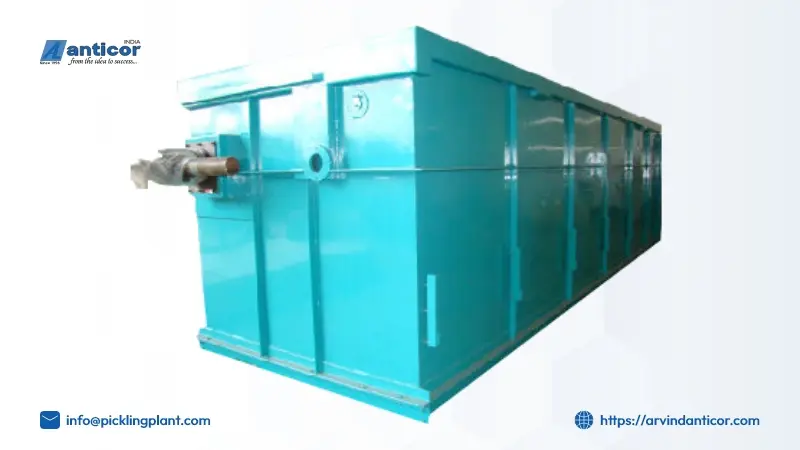
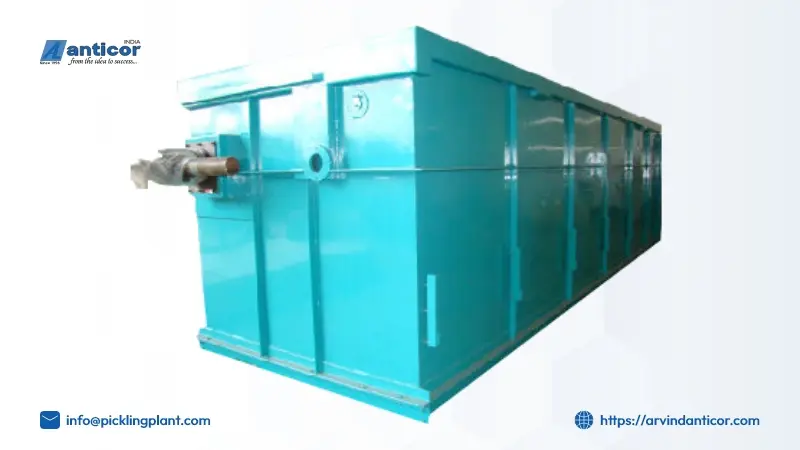
Hot-dip galvanizing is a process of applying a protective zinc coating to steel or iron materials to prevent rusting and corrosion.
Galvanizing works by forming a protective zinc coating around the base metal through a metallurgical bonding process. When the zinc meets the steel surface, a series of zinc-iron alloy layers are formed which permanently adhere to the steel providing a barrier that inhibits corrosion.
The hot-dip galvanizing process involves cleaning the steel surface, and then submerging the material in a bath of molten zinc at around 840°F. The zinc reacts and forms corrosion-inhibiting alloy layers with the steel.
When the steel is removed from the zinc bath, a final zinc coating is bonded to the steel through a series of distinct iron-zinc alloy layers.
In this blog post, we delve into the intricacies of hot dip galvanizing process, its benefits, and significance in modern construction and manufacturing industries.
What is Hot-Dip Galvanizing?
Hot-dip galvanizing is a process that involves coating iron or steel with a layer of zinc to prevent corrosion. During the hot-dip galvanizing process, parts are submerged in a bath of molten zinc. The zinc bonds with the metal substrate to form a corrosion-resistant coating of zinc-iron alloy layers.
The hot-dip galvanizing process provides a thick, durable, low-maintenance, and highly protective coating that can last for decades even in the harshest environments. The zinc coating forms a barrier between corrosive elements and the underlying base metal. If the coating gets scratched or damaged, the zinc will continue to provide cathodic protection and prevent corrosion from spreading.
Galvanized steel is commonly used in applications like buildings, automobiles, infrastructure, utility poles, fences, railings, street furniture, and many other steel products needing long-term corrosion resistance. The zinc coating protects against rust for decades, extending the lifetime of steel structures and components exposed to the elements.
Some key benefits of hot dip galvanizing plant include:
- Long-lasting corrosion protection can last over 50 years
- Low maintenance, no need for surface treatments or coatings
- Protects entire surface, coating wraps around all sides of steel
- Cost-effective for a lifetime of the structure
- Minimal surface preparation is needed compared to painting
- Tested & proven, used widely for over 150 years
- Recyclable material at end of life
- Meets high-quality standards for coating thickness & performance
Overall, hot-dip galvanizing transforms standard steel into a specialized corrosion-resistant building material perfect for long-term outdoor exposure. The metallurgically bonded zinc coating provides unmatched protection and durability for steel products.
Read Also: How to Set Up a Hot Dip Galvanizing Plant?
The Hot-Dip Galvanizing Process Step-by-Step
Hot-dip galvanizing is a multi-step coating process that protects steel from corrosion by applying a protective zinc coating. The hot-dip galvanizing process involves submerging cleaned steel into a bath of molten zinc to form a corrosion-resistant coating.
Properly following each step leads to a quality hot-dip galvanized coating that provides excellent corrosion protection for the underlying steel. Understanding the full galvanizing process helps ensure optimal coating performance. The main steps in the hot-dip galvanizing process are:
Step 1: Degreasing
Degreasing is the first step in the hot-dip galvanizing process and serves to remove oil, grease, drawing compounds, cutting fluids, and any other surface contaminants from the steel to ensure proper galvanizing. Effective degreasing ensures that the galvanizing zinc will properly adhere to the steel surface.
There are several methods used for degreasing:
- Alkaline cleaning uses heated alkaline cleaners like sodium hydroxide to react with fatty acids and transform oils and greases into water-soluble soaps that can be rinsed away. Tanks filled with alkaline solutions are used for immersion cleaning.
- Emulsion cleaning utilizes a combination of alkaline cleaners, emulsifiers, and water to lift insoluble oils off the surface and into the water. The steel is immersed in tanks filled with the emulsion solution.
- Solvent degreasing uses organic solvents like mineral spirits to dissolve and rinse away oil and grease deposits. Parts can be suspended above open tanks and sprayed with the solvent or immersed in enclosed tanks. Proper ventilation is critical when using volatile solvents.
- Steam cleaning directs high-pressure steam onto the steel surface to wash away oils and greases. Detergents can also be injected into the steam to boost cleaning power.
- Shot blasting propels tiny metal particles at the steel surface to provide abrasive cleaning and remove all traces of contaminants. This is a very effective surface preparation but doesn’t actually dissolve or rinse away oils and greases.
Whichever method is used, thorough degreasing is essential to ensure proper bonding between the steel and the galvanizing zinc layer that will protect it from corrosion.
Step 2: Rinsing
The purpose of rinsing after degreasing is to remove any remaining traces of the degreasing solution from the metal’s surface before it proceeds to the next step in the process.
The degreasing solution is an alkaline or acidic cleaning agent that breaks down and dissolves greases, oils, waxes, soil, and any other organic contaminants on the metal’s surface. Thorough rinsing is essential after degreasing to avoid carrying over any active chemical residue into the subsequent process steps.
Rinsing is typically done by spraying or immersing the metal in a cascade of fresh water. The rinse water may be cold or heated to increase effectiveness. Using a high-pressure water spray can help ensure the metal surface is fully cleaned by mechanical action.
Proper rinsing prevents staining or unintended reactions with the pickling solution later on. Any remaining traces of the alkaline or acidic degreaser could interfere with the acid pickling process, reducing its efficiency. The rinse water must remove the degreasing agent down to negligible levels through dilution and flushing action.
Rinsing also helps prepare the metal’s now clean surface for the optimal pickling action in the next step. Thorough rinsing provides a blank slate for the acid pickle to remove metal oxides and scales while minimizing the drag-in of impurities from the degreasing process. This allows for more controlled and uniform pickling across the entire metal surface area.
The rinsing stage is a quick but crucial intermediary step that removes all residual degreasing chemicals through freshwater flushing. Proper rinsing prevents cross-contamination between process steps and sets up the metal surface for effective scale removal via pickling.
Step 3: Pickling
Pickling, also known as acid etching, is a critical step in the hot-dip galvanizing process. The primary purpose of pickling is to remove any remaining rust, mill scale, and surface imperfections from the steel to prepare it for the hot-dip galvanizing bath.
Pickling uses an acid solution to clean and etch the surface of the steel. The most common acids used are hydrochloric acid (HCl) and sulfuric acid (H2SO4). Using an acid solution removes contaminants and etches the surface to enable excellent metallurgical bonding between the molten zinc and steel during the hot-dip galvanizing process.
The pickling acids and time exposure depend on the grade of steel. Low-carbon steels are pickled in sulfuric acid for 2-10 minutes. High-strength or alloy steels require hydrochloric acid pickling for 5-20 minutes. The acids are used at concentrations between 5-22% and heated up to 145°F.
Proper pickling is essential so the liquid zinc can spread evenly and adhere metallurgically to the steel during galvanizing. This creates a protective zinc coating that provides corrosion resistance and prevents rusting of the base steel.
Step 4: Rinsing After Pickling
After the steel undergoes pickling to remove any iron oxides or scale, it must be thoroughly rinsed again. Rinsing after pickling serves a crucial purpose in the hot-dip galvanizing process.
The acidic pickling solution must be completely rinsed off to prevent contamination of the molten zinc bath. Any acidic residues left on the steel will react adversely when immersed in the hot zinc, potentially causing issues like water entrapment, wetting problems, or dross formation. Effective rinsing also prevents potential problems with the fluxing process.
Fresh water is used to rinse off the spent pickling solution. The rinsing is done very thoroughly to make sure no traces of acid solution remain. The steel must be completely neutralized before moving to the next steps of pre-fluxing and hot-dip galvanizing. Multiple rinse tanks may be used to achieve a proper neutral pH.
Thorough rinsing after pickling is an essential part of the hot dip galvanizing plant process. Proper rinsing technique helps ensure quality coating results. The steel must be completely free of acidic pickling residue before undergoing fluxing and dipping in the molten zinc bath. Taking the time to properly rinse the steel prevents many potential quality issues.
Step 5: Pre-Fluxing
Pre-fluxing is an important step right before the galvanizing process. It involves applying a molten flux coating to the metal surface. This flux coating serves several key purposes:
- It facilitates wetting of the steel surface so that the molten zinc can spread evenly over the metal during galvanizing. Without pre-fluxing, the zinc may not properly adhere.
- It cleans and further etches the metal surface. The flux removes any residual oxides or soils that may still be present after pickling.
- It prevents re-oxidation of the cleaned metal surface before it enters the zinc bath. The flux coating protects the reactive metal surface.
- It prevents impurities from entering the zinc bath. The flux forms a protective coating that blocks any oils, soils, or iron fines from entering the molten zinc.
The flux is composed of zinc chloride, ammonium chloride, and other proprietary ingredients. It has a low melting point and becomes molten when heated to around 140–160°C. At this liquid state, the flux can be readily applied across the metal surface. Its composition and properties are precisely controlled to enable it to serve its key roles in the galvanizing process.
Step 6: Galvanizing
The key step in the hot-dip galvanizing process is the immersion of the steel into the molten zinc bath. This bath contains over 98% zinc with small amounts of other metals like aluminum and nickel.
The bath is maintained at temperatures ranging between 815-870°F (435-465°C). The base steel must be fully immersed in the bath for sufficient coating thickness. Immersion time depends on the thickness of the steel but is usually 1-5 minutes.
Thicker steel requires a longer immersion time. As the steel is immersed, a series of zinc-iron alloy layers are formed on the surface of the steel which provides excellent corrosion protection. The top layers of the coating are pure zinc which further enhances corrosion resistance.
Proper bath temperature and immersion duration are critical for quality galvanized coating and corrosion protection over the lifetime of the steel. The molten zinc reacts with the iron in the steel to form a metallurgical bonded coating.
Step 7: Finishing
The final step in the hot-dip galvanizing process involves inspecting and finishing the galvanized product. Once the steel part is removed from the zinc bath, it undergoes a series of post-treatment processes:
- Cooling – The galvanized part is cooled either by air or water quenching. Air cooling allows the zinc coating to develop its characteristic spangled appearance.
- Flux removal – Any residual flux on the part is removed by water washing, mechanical brushing, or air knifing. This prevents staining and promotes coating passivation.
- Inspection – The quality and thickness of the zinc coating are carefully inspected. Parts that fail to meet specifications can be reworked or stripped and re-galvanized if needed.
- Passivation – The galvanized coating is often passivated using a chromate solution. This forms a thin protective film to enhance corrosion resistance.
Proper finishing ensures the galvanized coating has good adhesion, and uniform appearance and meets the required coating thickness standards. The final inspection verifies the quality of the galvanized coating before the steel parts leave the galvanizing plant.
Conclusion
This comprehensive guide has shed light on the intricate process of hot-dip galvanizing, highlighting its significance, benefits, and applications across various industries. Understanding the meticulous steps involved in this process is crucial for ensuring the longevity and durability of metal products. For top-quality hot-dip galvanizing services, look no further than hot-dip galvanizing plants like Arvind Anticore, one of the leading manufacturers in India.
Embrace the protection and strength that hot-dip galvanizing offers, and trust in reputable providers like Arvind Anticor for all your galvanizing needs.
Let’s Connect
Contact Us
We are live 24/7 and reply within 48 hours.
Get in Touch
-
-
-
Address
Survey No.584/1+2 – C,Nr. Akshar Industrial Estate Mahemdabad Highway Road,Vatva Ahmedabad-382445, Gujarat, India.