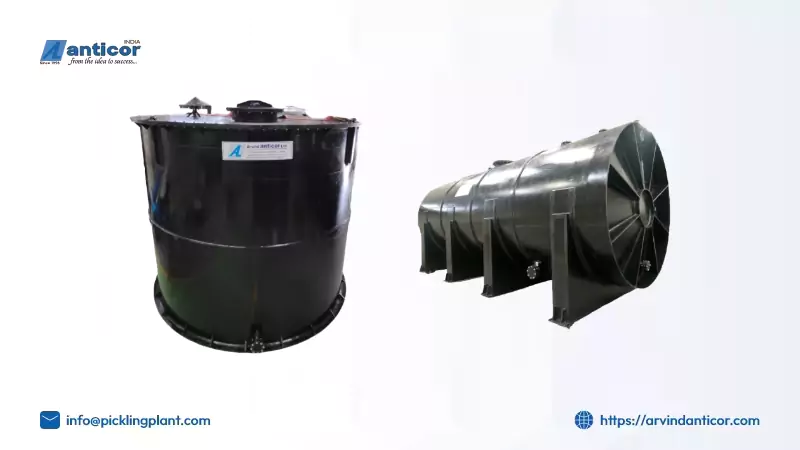
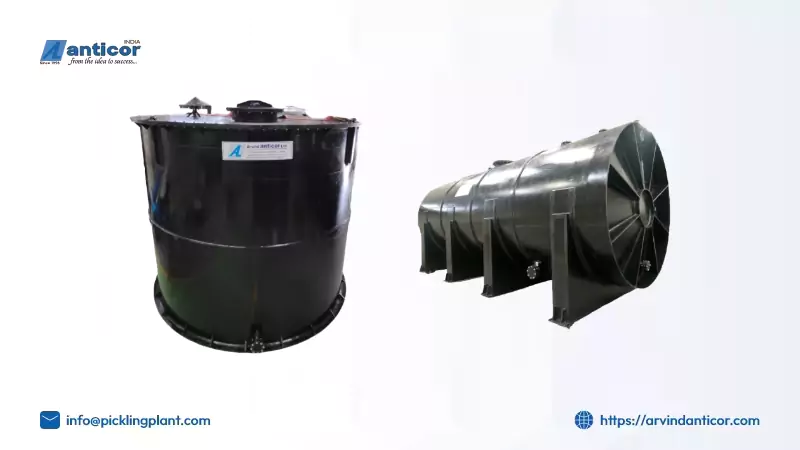
Hey there, have you ever wondered about the specifics of chemical storage tank ventilation? If you deal with hazardous chemicals in your line of work, proper ventilation is critical for safety and compliance. You need to make sure toxic fumes and vapors are properly extracted to avoid exposure risks. But how do you determine if your current ventilation setup is adequate or if it needs improvement? This article will walk you through the key ventilation guidelines for chemical storage tanks so you know to assess if your systems are up to par.
Take a deep breath – this is important stuff, but we’ll break it down in an easy-to-understand way. Let’s get started!
General Chemical Storage Guidelines
When storing chemicals in tanks, proper ventilation is key to safety.
Provide exhaust ventilation
Exhaust vents pull hazardous fumes out of the storage area to prevent buildup. Place exhaust vents at the top of tanks since fumes rise. Run vents to the outside, not just to another room. Use explosion-proof fans rated for the chemicals you’re storing.
Include makeup air
As air is exhausted, it must be replaced. Makeup air vents bring in fresh air from outside. Place them at the bottom of tanks opposite exhaust vents. The number and size of makeup air vents should match exhaust vents so air pressure remains balanced.
Follow guidelines for the type of chemicals.
The level of ventilation needed depends on the chemicals. Volatile, flammable, or highly toxic chemicals require the highest ventilation rates. Check safety data sheets for each chemical to determine requirements. It’s best to assume the highest levels to be safe.
Inspect vents and fans regularly to ensure proper operation. Test the entire ventilation system upon installation and periodically thereafter, especially if any changes have been made. Make any necessary repairs or adjustments right away.
Proper ventilation, with both exhaust and makeup air, is essential for storing chemicals safely in tanks. Following guidelines based on the specific chemical storage ventilation, regularly inspecting the system, and testing to ensure maximum efficiency will help reduce risks like fire, explosion, or exposure. Your facility, employees, and the environment will be better protected when you make ventilation a priority.
Ventilation Methods for Different Tank Types
When it comes to ventilation, the type of chemical storage tanks ventilation you have determines the methods you’ll need to use.
Fixed roof tanks
These are the simplest tanks but also the most prone to emissions since they lack any internal floating roof or seal. You’ll want a balanced pressure vacuum vent to prevent the tank from collapsing or bursting. Capture and control the emissions from these vents to limit pollution.
Floating roof tanks
Internal floating roofs (IFR) rise and fall with the liquid level, preventing vapor buildup. They require rim vents and gage hatches for access which must have vapor recovery units.
External floating roofs (EFR) have a roof that floats on the surface of the stored liquid. They need roof drain vents, gage wells, and stub drains for temperature variations. Connect these openings to vapor recovery equipment.
Domed roof tanks
Geodesic domes are highly effective for emissions control since the dome roof geometry is ideal for preventing vapor build-up. They only require pressure-vacuum relief vents and gauge hatches – attach these to vapor recovery systems. Using the proper ventilation method for your specific storage tank is vital for managing hazardous emissions and complying with environmental regulations. The right choice can drastically cut pollution from these industrial operations and make the area safer for all. With some forethought in the design and equipment selection process, storage tank ventilation can be quite straightforward to implement.
Read Also: Different Types of Chemical Storage Tanks
Requirements for Specific Storage Ventilation
Ventilation for chemical storage tanks is crucial to maintaining a safe working environment and complying with regulations. The specific chemical storage ventilation requirements for each tank depend on the chemicals being stored.
Flammable Liquids
For tanks containing flammable or combustible liquids like acetone, ethanol, or benzene, ventilation aims to prevent the buildup of flammable vapors. Provide ventilation at a rate of at least 1 cubic foot per minute (cfm) per square foot of tank area, with a minimum of 150 cfm. Vent vapors to a safe location away from air intakes and ignition sources. Spark-proof fans and explosion-proof electrical equipment should be used wherever there is a risk of flammable atmospheres.
Corrosive Chemicals
These substances like acids and bases release vapors that can damage equipment and irritate the lungs. Aim for at least 6 air changes per hour for tanks storing corrosive chemicals. The ideal approach is to vent corrosive vapors at their source before they can disperse into the surrounding area. Scrubbers or neutralization systems may be required for some chemicals.
Toxic Gasses
For tanks containing toxic gasses such as ammonia, chlorine, or sulfur dioxide, the goal is to prevent hazardous concentrations from accumulating. Follow the recommendations in the Safety Data Sheet (SDS) for the specific chemical. Often 10-15 air changes per hour or more are required. Consider using air monitoring equipment to ensure safe levels. Vapor containment or scrubbing may be necessary in some situations.
Maintaining proper ventilation for chemical storage tanks is a complex task, but it’s essential for the health and safety of your workers as well as environmental protection. Always follow the guidelines for your chemical storage ventilation requirements accordingly. When in doubt, increase ventilation and monitor the air to confirm safe conditions.
Ventilation System Maintenance Tips
To keep your ventilation system running efficiently, follow these maintenance tips:
Inspect and Clean Regularly
Inspect your ventilation system regularly, at least once a month. Check that all fans are running properly and the air is flowing as intended. Clean or replace any clogged or dirty air filters. Built-up dust and debris reduce airflow and the system’s effectiveness.
Lubricate and Tighten
Lubricate any moving parts like fan blades or dampers to prevent squeaking and ensure optimal performance. Tighten any loose screws or bolts to minimize vibration and noise. Lack of lubrication and loose parts will degrade the system over time.
Test Emergency Equipment
If your system includes emergency equipment like backup generators or exhaust fans, test them regularly to confirm they will operate properly in a crisis. Run generators at least once a month for 30 minutes. Activate exhaust fans to verify the blades spin at full speed. Non-functioning emergency equipment puts facilities and personnel at risk.
Inspect Ductwork and Piping
Inspect any ductwork, piping, valves, or flanges connected to the ventilation system. Look for signs of damage, corrosion, leaks, or blockages that impede airflow. Repair or replace compromised components immediately to avoid contamination or unsafe conditions.
Keep Records
Document all maintenance, testing, and repair activities to confirm regulatory compliance and for system performance evaluation. Note runtime hours for major equipment like generators or exhaust fans. Updated records should be kept for the lifetime of the ventilation system.
By establishing a routine maintenance plan and schedule, and diligently performing the necessary inspections, cleaning, and repairs, you’ll optimize your ventilation system’s performance and help ensure a safe working environment. Staying on top of maintenance also allows you to identify any issues early and avoid costly emergency repairs down the road.
Conclusion
So there you have it. By following these ventilation guidelines and best practices for your chemical storage ventilation, you’ll help ensure the safety of your facility and everyone in it. Proper ventilation is not just a recommendation, it’s the law. Staying on top of the latest regulations and making sure your systems are up to code is part of responsible chemical management and storage. By doing so, you not only safeguard your facility and its occupants but also contribute to a safer community and environment. Trust Arvind Anticore for reliable solutions and peace of mind. Stay safe out there!
Let’s Connect
Contact Us
We are live 24/7 and reply within 48 hours.
Get in Touch
-
-
-
Address
Survey No.584/1+2 – C,Nr. Akshar Industrial Estate Mahemdabad Highway Road,Vatva Ahmedabad-382445, Gujarat, India.