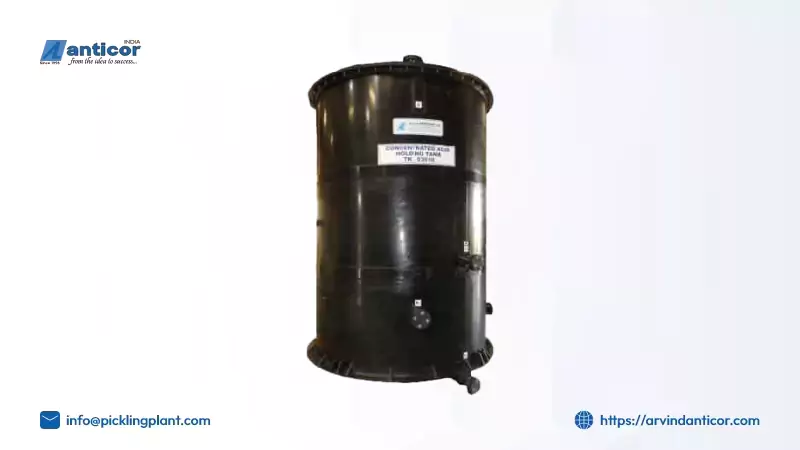
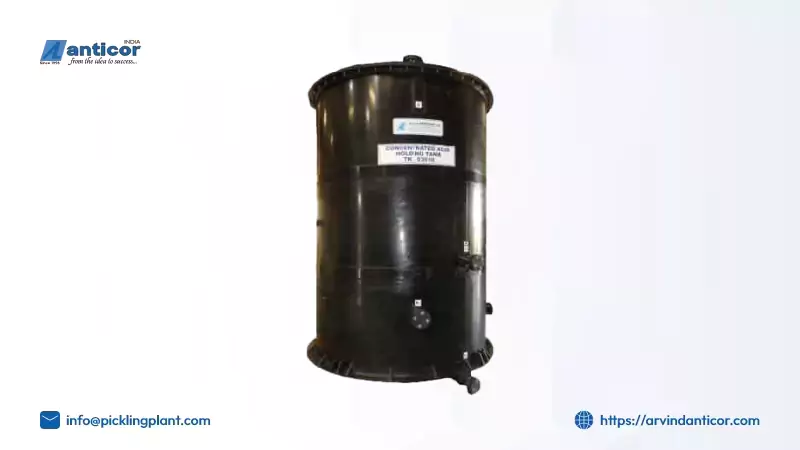
So you’ve got some dangerous chemicals you need to store, and you’re wondering about using a tank within a tank system. Makes sense – double containment means double the safety, right? Well, sort of!
There are some real upsides to tank-in-tank storage, but there are also a few downsides you should be aware of before moving forward. On the plus side, if your primary storage tank springs a leak for any reason, the secondary containment tank catches everything, avoiding spills and keeping your chemicals safely contained.
It also adds an extra layer of protection against the weather. However, tank-in-tank is not a perfect solution. It requires more space, costs more to install and maintain, and makes inspecting and accessing your primary tank trickier. There’s a lot to consider here.
Before you dive in and invest in one of the best systems for chemical storage tank types demands, let’s go through the main advantages and disadvantages so you can make the most informed, risk-free decision possible.
What Is Secondary Containment in Chemical Storage?
Secondary containment in chemical storage refers to containing chemicals in two separate but integrated storage tanks. The inner tank stores the chemicals, while the outer tank provides an additional layer of containment in case the inner tank leaks or ruptures.
If you’re storing large volumes of chemicals, secondary containment is a must for safety and compliance. It helps prevent chemicals from spilling and contaminating the surrounding area. The outer tank contains any leaks from the inner tank, allowing you to detect and address issues before catastrophe strikes.
The Pros of Using a Tank within a Tank System
A tank within a tank system provides the ultimate protection for secondary containment in chemical storage. Here are some of the major pros of using this type of containment:
Superior containment
Having a secondary tank surround your primary storage tank, essentially gives you double the protection. If there’s a leak in the inner tank, the chemical is captured in the outer tank before it has a chance to contaminate the environment. Peace of mind that your chemicals are securely contained.
Flexibility
A tank within a tank gives you options. You can choose tanks made of different materials – for example, an inner tank made of stainless steel within an outer concrete tank. This allows you to select the best material for your specific chemical. You also have more choices in tank sizes to suit your needs.
Easy to access and maintain
Unlike underground storage tanks, a tank within a tank system is accessible, allowing for routine inspections, maintenance, and repairs. You can visually check the condition of both tanks and identify any issues early on before they become a bigger problem. Performing maintenance and repairs on an above-ground, double-walled tank is also much easier and more cost-effective.
Satisfies regulations
Many local regulations require secondary tanks in chemical storage for hazardous chemicals. A tank within a tank meets and exceeds these requirements, ensuring you stay in compliance. Your facility and employees will be adhering to safety standards, and your company will avoid potential fines and violations.
A tank within a tank system may require a higher upfront investment, but the added security, flexibility, accessibility, and compliance provide substantial value over the lifetime of your storage tanks. For safely storing chemicals, two tanks are better than one.
The Cons of Using a Tank within a Tank System
While a tank within tank systems seems ideal in theory, there are some downsides to consider:
Cost
Tank within a tank containment system tend to be significantly more expensive than standard single wall tanks. You’re essentially paying for two tanks, plus the cost of the interstitial space in between and any monitoring equipment. For small operations with tight budgets, the upfront cost can be prohibitive.
Reduced Capacity
The secondary containment in chemical storage takes up volume, so you lose some of the capacity of the primary tank. If maximizing storage volume is a priority, a tank within a tank system may not be the most efficient choice. You’ll need a larger overall footprint to store the same amount of chemicals as a single wall tank.
Additional Maintenance
There are more components to inspect and maintain with a double wall tank. You need to routinely check the interstitial space for any leaks as well as the integrity of both the primary and secondary containment tanks. Monitoring equipment also requires calibration and upkeep. The extra maintenance required can mean higher operating costs over the lifetime of the system.
Difficulty Repairing or Replacing
If there is damage to either tank, repairs or replacement can be complicated by the presence of the other tank. Removing one tank usually means removing the other, and welding or other repair work on the inner tank needs to be done carefully to avoid harming the outer tank. This can lead to longer downtime and higher repair or replacement costs.
While a tank within a tank containment does have significant safety and environmental benefits, the additional costs, reduced storage capacity, extra maintenance, and challenges with repair or replacement are factors to weigh based on your needs and budget. For some operations, a single wall tank with strong spill containment, leak detection, and an impermeable floor and walls may provide sufficient protection at a lower overall cost.
Best Practices for Choosing and Implementing Secondary Containment
There are various recommended practices to consider while selecting and establishing secondary tanks in chemical storage for hazardous compounds. These practices assure regulatory compliance and aid in the prevention of spills and leaks that can harm the environment and human health. Here are some crucial items to remember:
Choose Compatible Materials
Make sure the materials used for the best chemical storage tank types are compatible with the chemical(s) being stored. For example, do not use steel for a tank within a tank system for chemicals like caustics, as it can corrode the steel. Fiberglass, polyethylene, or coated steel are better options.
Proper Size Ratio
The secondary containment tank should be large enough to hold at least 110% of the volume of the primary tank. This provides enough containment in case of a leak or spill from the primary tank. Some local regulations may require an even larger containment ratio, so check with agencies in your area.
Durable and Chemical-Resistant
The secondary containment tank must be made of a durable material that can withstand exposure to the stored chemical. It should not crack or weaken when in contact with the chemical. High-density polyethylene (HDPE) and fiberglass are excellent choices for chemical resistance and durability.
Regular Inspections
Conduct routine inspections of the primary tank, secondary containment, and any connections or piping between them. Look for any signs of damage, leaks, or spills that could compromise the system. Make any necessary repairs immediately to ensure maximum protection.
Proper Drainage
The secondary tanks in chemical storage should have a way to drain collected rainwater or spills, such as a drain valve at the lowest point. This allows you to empty the containment tank so it is ready in case of any future leaks or releases from the primary tank. Close and secure the drain valve when the containment tank is empty.
Following these best practices will help you choose and implement a safe, secondary containment in chemical storage for your facility. Be sure to also follow all regulations and choose from the best chemical storage tank manufacturers, you can ensure the safe storage of hazardous materials in your facility.
Final Thoughts
In conclusion, using a tank within a tank for chemical storage has its pros and cons. While it provides an extra layer of protection and containment, it also comes with additional costs and hassles. Ultimately, the decision depends on your specific situation and needs. If you’re looking for a chemical storage solution, Arvind Anticor offers a range of chemical storage solutions, including conical chemical storage tanks with secondary containment features. Request a free consultation with Arvind Anticor to discuss your chemical storage needs and find the right solution for your business.
Let’s Connect
Contact Us
We are live 24/7 and reply within 48 hours.
Get in Touch
-
-
-
Address
Survey No.584/1+2 – C,Nr. Akshar Industrial Estate Mahemdabad Highway Road,Vatva Ahmedabad-382445, Gujarat, India.