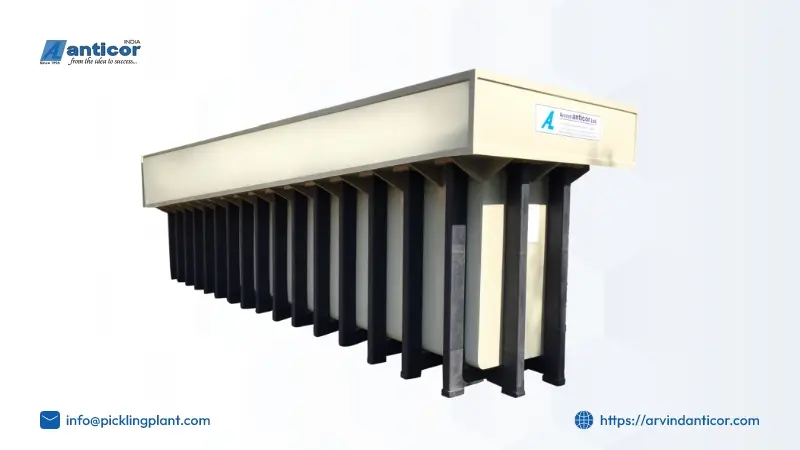
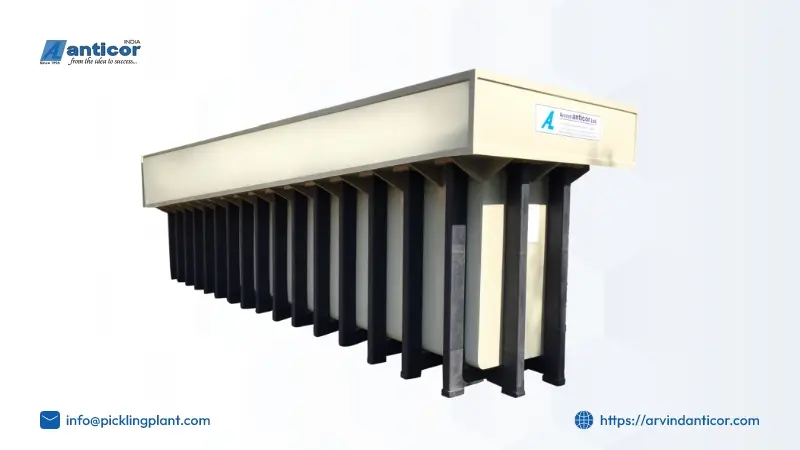
Industrial procedures utilize large pickling tanks to remove impurities, scale and corrosion from metal surfaces. The majority of these tanks are composed of high-quality plastics.
Various types of pickling tanks are essential to the corrosion process because they provide an acid solution with a secure and controlled environment. They can easily withstand the acid’s corrosive nature. In addition, manufacturers tailor them to meet the specific requirements of various industries. They vary in size and shape, including rectangular, cylindrical, and conical, based on the type of metal parts being pickled and the amount of acid solution required.
We can see pickling tank applications in numerous industries, including steel manufacturing, the automotive industry, the aerospace industry, and the construction industry. They are essential for preserving the quality and durability of metal components and ensuring that they are free of any impurities that could hinder their performance.
Pickling Tanks Types and Applications
In pickling tanks, the workers pickle, passivate and clean copper, brass and other alloys using acid. Manufacturers customize various types of pickling tanks to meet specific industrial requirements. The following are some common types of pickling tanks:
1. PP Pickling Tanks
The exceptional chemical resistance of Polypropylene (PP) pickling tanks makes them suitable for pickling applications involving various acids, alkalis, and other corrosive substances. PP is renowned for its resistance to impact and tension fractures, making it a lightweight material.
These tanks can withstand temperatures up to 100°C, making them suitable for pickling processes that require heating the acid solution. Additionally, adding fittings, drainage, and other accessories readily modifies PP pickling tanks to meet specific needs.
Metal refining, galvanizing, and semiconductor manufacturing are common PP pickling tanks applications. In metal refining and plating, PP pickling tanks are used to remove surface impurities from metals prior to plating. The semiconductor industry utilizes them to etch and polish silicon substrates.
PP pickling tanks are an excellent option for pickling applications requiring chemical resistance, durability, and the capacity to withstand high temperatures.
2. FRP Tanks
FRP pickling tanks are composite materials composed of fiberglass and a thermosetting resin. This combination produces a tank that is highly resistant to corrosion and chemical deterioration, as well as robust and long-lasting. Custom sizes, shapes, and wall thicknesses are available for FRP pickling tanks types to accommodate specific industrial requirements, including cylindrical, conical, square, rectangular and flat.
FRP pickling tanks are superior to other varieties of pickling tanks in a number of ways. They are portable and simple to implement due to their reduced weight. Additionally, they are highly UV-resistant, making them suitable for outdoor use. In addition, FRP pickling tanks have a longer longevity than tanks made from other materials, making them a cost-effective option for industries that require pickling tanks.
In industries including metal finishing, automotive, aerospace, and construction, FRP pickling tanks applications take place for the pickling and cleansing of metals such as steel, copper, and aluminum. The chemical industry also uses FRP pickling tanks for the storage and management of acids and other corrosive materials.
3. HDPE Pickling Tanks
HDPE pickling tanks frequently store and handle highly corrosive chemicals such as sulphuric acid, phosphoric acid, hydrochloric acid and others. These tanks, made of high-density polyethylene, exhibit resistance to corrosion, impact and extreme temperatures. This makes them suitable for a vast array of applications in a variety of industries.
Various industries, including metal refining, chemical processing, and steel, commonly utilize HDPE pickling tanks. For instance, the metal refining industry uses these tanks to remove oxides and other impurities from metal surfaces. Similarly, the steel industry employs pickling tanks for acid washing and surface preparation of steel products.
Not only this, the chemical processing industry uses HDPE pickling tanks to store and transport highly corrosive compounds safely. Additionally, the pharmaceutical industry uses various HDPE pickling tanks to disinfect and sterilize apparatus and instruments.
Along with chemical resistance, HDPE pickling tanks are durable and long-lasting. They can withstand extreme conditions and are resistant to splitting and deformation. This makes them a cost-effective and dependable option for the storage and management of corrosive compounds.
4. Stainless Steel
Pickling tanks typically consist of 304 or 316-grade stainless steel. They are highly resistant to corrosion. These tanks are capable of handling a variety of corrosive solutions, such as hydrochloric, nitric and sulfuric acid. They can also withstand temperatures up to 200 degrees Celsius.
Durability is one of the primary benefits of stainless steel pickling tanks type. They can withstand severe industrial environments and, with appropriate care, can last for many years.
The pharmaceutical, food processing and chemical industries widely use stainless steel pickling tanks for various applications. They are excellent for refining metals like steel and aluminum and producing compounds like fertilizers and pesticides. They are also utilized in the production of dairy products, and liquids.
5. Rubber-lining Pickling Tanks
Rubber-lined pickling tank types are the ones whose interior surface is lined with rubber to provide additional corrosion prevention. Rubber-lining pickling tanks applications take place where the temperature does not surpass 80 degrees Celsius. The chemical industry frequently uses them for pickling and storing acids. Moreover, the manufacturing industry employs them for pickling and cleansing metal components.
The ability of rubber-lined pickling tanks to withstand a variety of chemical compounds, including hydrochloric acid, sulfuric acid, and phosphoric acid, is one of their primary advantages. The rubber interior also provides exceptional abrasion resistance, making these tanks an excellent choice for pickling applications.
Conclusion
For companies that depend on industrial processes involving pickling acids, investing in the right pickling tank types is essential. These acids are extremely corrosive and may cause wear and tear on process-related apparatus and materials. Thus, pickling tank manufacturers in India like Arvind Anticor have developed various types of pickling tanks that provide sufficient corrosion and chemical damage protection.
Let’s Connect
Contact Us
We are live 24/7 and reply within 48 hours.
Get in Touch
-
-
-
Address
Survey No.584/1+2 – C,Nr. Akshar Industrial Estate Mahemdabad Highway Road,Vatva Ahmedabad-382445, Gujarat, India.