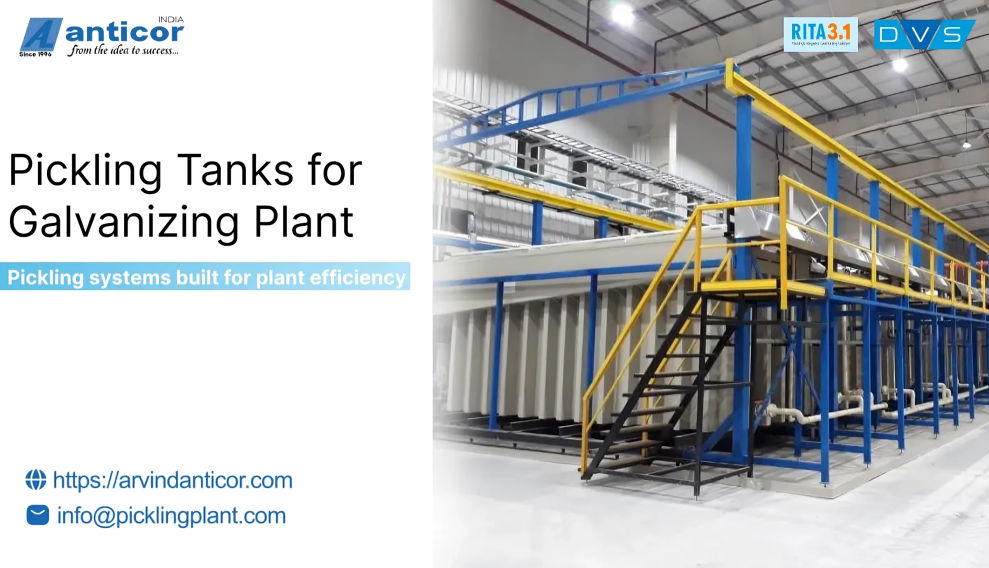
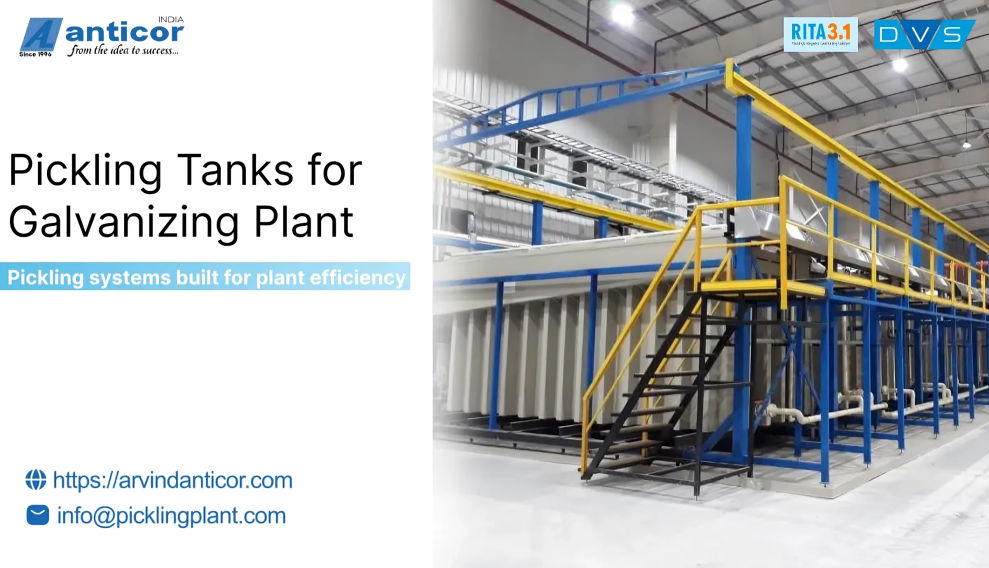
Galvanizing plants depend heavily on precise surface treatment processes to deliver high-quality, corrosion-resistant steel products. At the heart of these processes are pickling tanks, which are essential for preparing steel surfaces before the hot-dip galvanizing stage. Understanding their function is key to improving performance, compliance, and cost-efficiency in any galvanizing operation.
For a deeper understanding of the overall galvanizing process, check out our detailed guide on What Is Hot-Dip Galvanizing and Its Process.
The Role of Pickling Tanks in a Galvanizing Plant
In a galvanizing plant, steel must undergo thorough surface preparation before it can be effectively coated with zinc. This is where pickling tanks come into play. These tanks are used to clean steel using acid solutions such as hydrochloric or sulfuric acid. The goal is to remove mill scale, rust, and other contaminants that would otherwise interfere with the zinc coating process.
Without proper pickling, the steel surface will not bond well with the zinc, resulting in poor adhesion, uneven coating, and reduced corrosion resistance—undermining the entire purpose of the galvanizing plant.
Why Every Galvanizing Plant Needs High-Quality Pickling Tanks
1. Crucial to Steel Surface Preparation
Pickling tanks are the starting point of the galvanizing process. In any galvanizing plant, these tanks ensure that steel enters the zinc bath in a perfectly clean state, maximizing coating quality and longevity.
2. Built for Corrosive Environments
A galvanizing plant deals with harsh chemicals and high temperatures. Pickling tanks made from PP (Polypropylene), HDPE, or FRP are engineered to resist corrosion, ensuring safety and extended service life under extreme conditions.
At Arvind Anticor, we manufacture tanks using DVS welding standards and precision tools like RITA 3.1 software to ensure chemical integrity and dimensional accuracy.
3. Improved Plant Efficiency and Cost Savings
Efficient operations are key to a successful galvanizing plant. High-quality pickling tanks reduce the need for frequent maintenance, lower downtime, and minimize the risk of acid leakage—saving you both time and operational costs.
4. Custom-Built for Your Galvanizing Plant Layout
Every galvanizing plant is unique, and so are its infrastructure requirements. Custom-fabricated pickling tanks can be designed to suit your workflow, optimize space, and integrate seamlessly with your acid fume extraction systems and material handling equipment.
5. Environmentally Compliant
With increasing environmental regulations, modern galvanizing plants must control emissions. Pickling tanks, when paired with efficient acid fume extraction systems, help manage and neutralize hazardous emissions, contributing to safer workspaces and regulatory compliance.
Material Handling Systems in Galvanizing Plants
An often overlooked but vital element adjacent to pickling operations is the material handling system. In a galvanizing plant, ensuring smooth and safe movement of steel parts through different stages—from pickling to fluxing to galvanizing—is critical. Manual handling not only slows production but increases the risk of accidents and damage.
Mechanical and automated material handling systems, such as cranes, hoists, and conveyors, ensure precise and safe transfer of components between tanks and workstations. This integration improves workflow, reduces labor costs, and increases overall efficiency. Arvind Anticor provides material handling solutions tailored to your galvanizing plant’s layout, ensuring perfect synchronization with pickling tank operations.
Choosing the Right Material for Your Galvanizing Plant’s Pickling Tanks
Material selection is vital. At Arvind Anticor Limited, we provide customized pickling tanks in materials best suited for galvanizing plants:
- Polypropylene (PP): Excellent chemical resistance and temperature stability.
- FRP (Fiber Reinforced Plastic): High strength, durability, and structural integrity.
- HDPE (High-Density Polyethylene): Cost-effective with good acid resistance and durability.
Each material supports specific needs based on the size, temperature, and acid concentration of your pickling process.
Final Thoughts: Investing in the Future of Your Galvanizing Plant
To achieve consistent, high-quality galvanization, every galvanizing plant must start with clean, properly prepared steel — and that begins in the pickling tank. Investing in durable, well-designed tanks tailored to your operational requirements is one of the smartest decisions you can make for the long-term success of your plant.
For expert guidance on setting up a galvanizing facility, don’t miss our blog on How to Set Up a Hot Dip Galvanizing Plant: Expert Tips.
At Arvind Anticor, we bring decades of engineering expertise, international quality standards, and proven material technologies to every pickling tank we build. Let us help you enhance the safety, efficiency, and performance of your galvanizing plant.
Let’s Connect
Contact Us
We are live 24/7 and reply within 48 hours.
Get in Touch
-
-
-
Address
Survey No.584/1+2 – C,Nr. Akshar Industrial Estate Mahemdabad Highway Road,Vatva Ahmedabad-382445, Gujarat, India.