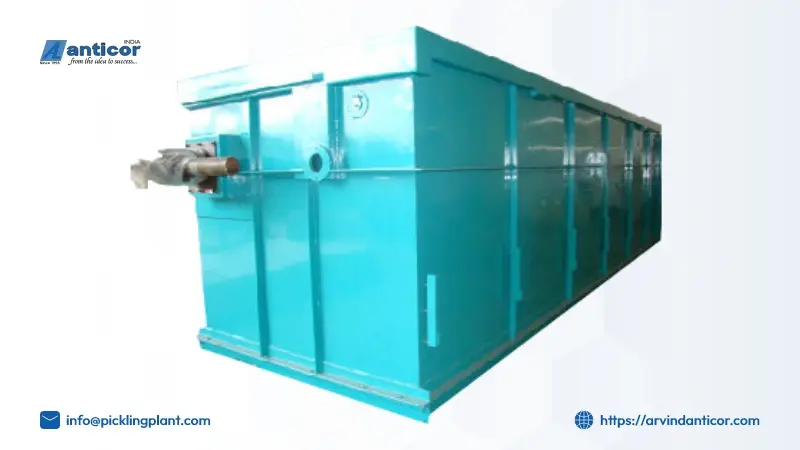
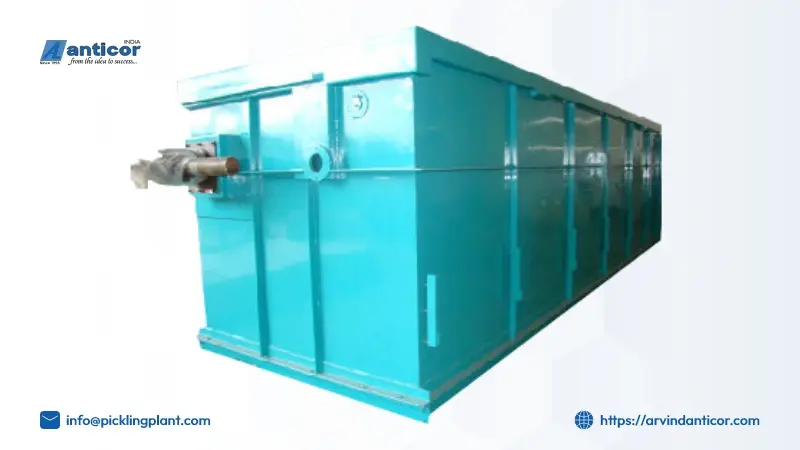
Ever wanted to start your own hot dip galvanizing plant? It may sound complicated but if you break it down into a few key steps, you’ll be coating steel in no time. The Pickling Tank For Galvanizing Plant process involves dipping steel or iron in a bath of molten zinc.
This can result in a protective coating that prevents rusting and corrosion. Before you get started, there are a few things you need to know to set up your plant properly. We’ve got some top expert tips to help ensure your galvanizing operation is safe and produces high-quality results.
So grab your welding gear, fire up the furnace, and let’s get galvanizing! With a bit of knowledge and the right equipment, you’ll be providing corrosion protection for steel structures in your area in no time.
Selecting the Right Location and Building for Your Galvanizing Plant
So you want to set up your own hot dip galvanizing plant, ah? That’s great news! To get started, you’ll first need to find the right location and facility.
Look for industrial-zoned land in an area with minimal environmental restrictions. Galvanizing plants require handling permits which can be easier to obtain in certain industrial areas.
You’ll want a large building, at least 40,000 to 50,000 square feet, with high ceilings to accommodate the galvanizing kettle and overhead crane. Multiple bays for pre-treatment, galvanizing, quenching, and inspection are ideal. Steel-framed buildings stand up best to corrosive fumes.
Don’t forget ample space for raw material storage, finished product storage, and truck access for loading and unloading.
Ensure there are utilities in place to suit your power needs. Galvanizing kettles require a heavy-duty electrical supply, high-pressure natural gas lines, and wastewater treatment facilities.
Think about future expansion in your building design. Pickling tanks for galvanizing plants typically begin with a single kettle and grow to two or more kettles as output grows. Allow for additional bays, storage, and pre-treatment capacity from the get-go.
With the proper location and facility secured, you’ll be well on your way to establishing your thriving hot dip galvanizing plant. The keys are finding a space zoned and equipped for this type of industrial operation with room to grow over time.
Obtaining the Necessary Permits and Licenses
Setting up a Pickling Tank For Galvanizing Plant requires obtaining the proper permits and licenses to operate. This step can take time, so make sure to plan.
First, determine what permits and licenses apply to your area. These typically include air quality permits, wastewater discharge permits, and hazardous waste permits. The requirements vary in different countries and jurisdictions, so check with your local regulatory agencies.
Next, apply for the necessary permits and licenses. This usually involves submitting detailed plans for your facility that show how you will meet the required standards. The application process can take 6-18 months, so start early!
While waiting for approval, use the time to prepare your facility, train employees, and ensure you have the proper safety equipment and environmental controls in place. The regulators will inspect before granting final approval.
Once you have the green light, you’re ready to start production! But don’t forget that permits and licenses require periodic renewals and inspections to remain valid. Some may need to get renewed annually, while others are every few years.
Establishing a galvanizing plant is an exciting venture, but also highly regulated. You’ll set your business up for safe, legal, and productive operations by researching the requirements, applying well in advance, and maintaining compliance.
Choosing High-Quality Galvanizing Equipment
Selecting high-quality galvanizing equipment is key to setting up a successful hot dip galvanizing plant. The equipment you select will determine how efficient, safe, and productive your plant can be.
- Kettles
The kettle is where the hot dip galvanizing process takes place. Look for a kettle made of high-quality galvanized steel that can resist high temperatures. It also needs features like built-in temperature controls and automated zinc feeding systems.
- Handling equipment
To move materials in and out of the kettles, you’ll need heavy-duty handling equipment like cranes, hoists, conveyors, and lifters. Select equipment rated for high heat and chemical exposure. Look for automated or semi-automated options to minimize human contact with the molten zinc.
- Ventilation and emissions control
Proper ventilation and emissions control equipment is mandatory for a galvanizing plant. Fumes from molten zinc can be toxic, so you’ll need industrial exhaust fans, filters, and scrubbers to remove fumes and particulates.
- Protective gear
Don’t forget essential protective gear for your workers like zinc-resistant aprons and gloves, face shields, and other safety should be a top priority in your plant.
With the right equipment in place and a well-designed plant, you’ll be hot dip galvanizing materials efficiently in no time.
Setting Up the Pickling Tank for Galvanizing Plant
The Pickling Tank For Galvanizing Plant contains an acid solution that cleans and prepares the metal for the galvanizing process. So, setting up the pickling tank is one of the most important steps in getting your hot dip galvanizing plant up and running.
- Choosing the Right Tank
Select a tank made of acid-resistant materials like polyethylene or fiberglass-reinforced plastic (FRP). Steel tanks will corrode over time. The tank should be large enough to fully submerge your largest pieces. For most small to mid-sized galvanizing operations, a tank between 6 to 12 feet in diameter and 3 to 6 feet deep works well.
- Filling the Tank
Fill the tank with a diluted acid solution, typically hydrochloric acid (HCl) and water. A good starting point is a 10-15% HCl solution. Add the acid to the water slowly while stirring; never add water to the concentrated acid. The solution should be deep enough to fully submerge your workpieces.
- Removing Oxides and Impurities
The acid solution works by removing oxides, scale, rust, and other impurities from the surface of the metal through a chemical reaction. Check parts regularly as they soak and remove them once cleaned to avoid over-pickling.
- Rinsing and Drying
Remove parts from the pickling tank and rinse them thoroughly with water to remove any remaining acid solution. Allow parts to dry completely before immersing them in the molten zinc galvanizing bath.
Any trapped moisture will evaporate upon contact with the hot zinc, creating holes and bubbles in the galvanized coating.
Your galvanizing plant will have equally coated components in no time if you use the right tank, safety equipment, and pickling technique. Perform regular maintenance like acid skimming and tank scrubbing to prevent buildup.
Hiring and Training Qualified Staff
When setting up a hot dip galvanizing plant, hiring qualified staff is essential. The key positions you’ll need to fill include:
- Plant Manager
The plant manager oversees daily operations and manages employees. Look for candidates with experience managing industrial plants. Especially those involving hazardous materials and high-temperature processes like galvanizing. They should have strong leadership, communication, and problem-solving skills.
- Lead Galvanizer
The lead galvanizer supervises the galvanizing crew and galvanizing process. They should have several years of experience in hot dip galvanizing and knowledge of safety standards and procedures.
By hiring experienced managers and providing extensive on-the-job training for hands-on roles. You’ll assemble a knowledgeable team equipped to expertly and safely run your hot dip galvanizing plant. Continuous education and fair compensation will keep your staff motivated to do quality work.
Implementing Proper Ventilation and Safety Equipment
A proper ventilation system is critical for any hot dip galvanizing plant. Fumes from the molten zinc can be toxic, so you’ll need exhaust fans to pull the fumes away from workers and out of the facility. Consider installing a roof exhaust fan and wall exhaust fans around the kettle area.
To protect workers from heat, fumes, and hazardous materials, provide proper protective equipment like:
- Insulated gloves, jackets, pants, and aprons – for handling hot materials and withstanding radiant heat from the molten zinc.
- Respirators or fresh air masks – to avoid inhaling toxic zinc fumes. Disposable or half-mask respirators with acid gas cartridges are typically sufficient.
- Face shields – to protect eyes and face from splashes of molten zinc.
- Steel-toed boots – for general safety, especially when handling heavy equipment and materials.
- Hearing protection – the noisy, industrial environment requires ear plugs or noise-canceling headphones.
It’s critical to train all employees on equipment usage, emergency procedures, and workplace hazards. A safe and well-ventilated work environment can help prevent injuries, health issues, and downtime. Taking appropriate precautions will support quality production in your hot dip galvanizing plant.
Regularly Maintain and Repair Equipment
Maintaining and repairing your galvanizing equipment regularly is key to efficiency. Inspections are performed on a daily, weekly, monthly, and annual basis. Check things like seals, gaskets, valves, gauges, wiring, and safety mechanisms.
Tighten, replace, or repair anything that’s broken, worn, or not functioning properly. It’s much cheaper and safer to perform preventative maintenance rather than emergency repairs.
A buildup of zinc, flux, and other residues can impact performance and quality. Thorough cleaning also allows for full inspections to spot any issues early on.
Properly train all plant operators to safely run equipment, perform routine maintenance, and handle repairs. When new equipment is added or procedures change, training should be updated as needed. Enforce stringent safety measures and supply all staff with appropriate protective gear.
The best practices for equipment maintenance and repair will help ensure the consistency of hot dip galvanized coatings. Also, optimizing productivity reduces costs, and promotes a safe working environment for many years to come. With the proper care and upkeep, hot dip galvanizing equipment can provide decades of reliable service.
Conclusion
So now you know the key steps to setting up your own hot dip galvanizing plant. It may seem complicated at first, but if you follow the expert advice, and pay attention to the details, you’ll be dipping steel in molten zinc in no time. Running a galvanizing plant can be very rewarding work.
You get to provide a valuable service to businesses and customers while building something with your hands. If you go into this with passion, patience, and persistence, you’ll have a successful operation up and running before you know it. So what are you waiting for? Get out there and start galvanizing! The steel won’t coat itself.
Let’s Connect
Contact Us
We are live 24/7 and reply within 48 hours.
Get in Touch
-
-
-
Address
Survey No.584/1+2 – C,Nr. Akshar Industrial Estate Mahemdabad Highway Road,Vatva Ahmedabad-382445, Gujarat, India.