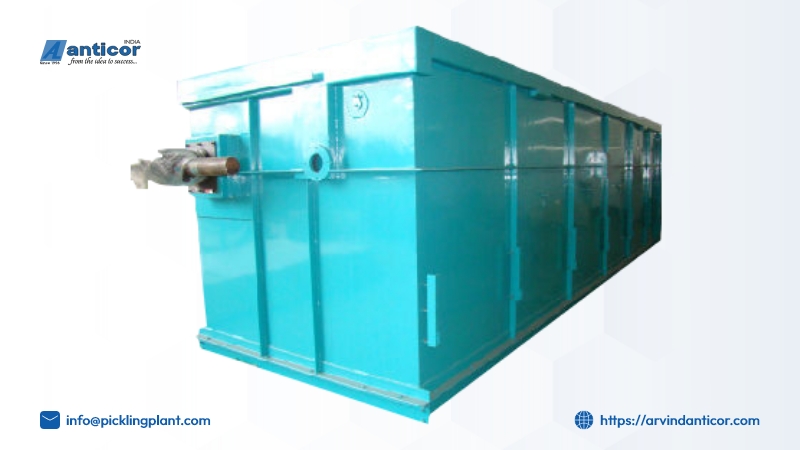
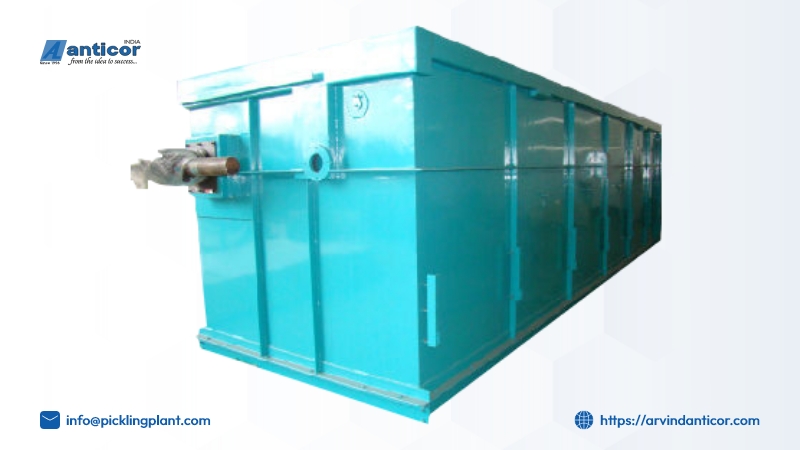
You must have heard the saying the chain is only as strong as its weakest link. Of course, as for hot dip galvanizing, the flux heating system also takes the position of the important factor. This one is a hot dip galvanizing process that involves submerging the products into a hot tank of molten zinc, in the process a metallurgical reaction takes place and a layer of zinc oxide is formed on the surface of the steel products.
Flux Heating Systems in Hot Dip Galvanizing plants are also essential in the control of heat in flux solution, which is a chemical solution that helps in removing the impurities on the surface of the metal and in achieving an even layering of zinc. Flux temperature is important in the operating efficiency of the galvanizing process; hence, the temperature of the flux solution must always be controlled.
In this blog post, we will explain how the flux heating system plays a crucial role in hot dip galvanizing plants and why it is necessary to choose the best flux heater. We will also be presenting the design aspects of flux heating systems and how they are implemented in waste heat recovery applications.
Overview of the Hot Dip Galvanizing Process
Hot dip galvanizing process entails dipping fabricated steel in the low viscosity molten zinc for the formation of the outer layer. This is the most effective method of protection against corrosion since it guarantees a metallurgical connection between the zinc and the steel.
This method is employed to protect the metal structures from rusting; the zinc acts as seasoning the iron to produce zinc oxide. The zinc oxide layer prevents the penetration and absorption of moisture and oxygen in the metal, hence reducing corrosion.
What is a Flux Heating System?
A flux heating system is an important feature of the hot dip galvanizing work. Most firms build structures with the inherent capability to regulate temperature to allow for fluxing in a proper manner.
The Flux Heating System in Hot Dip Galvanizing plant is very important in the galvanization process and is mainly used to regulate the temperature of the flux solution to a range of 60–80 °C. This temperature range is critical to achieving optimal operation of the galvanizing process and to generate a quality zinc coating that shields the steel from corrosion for an extended period.
Importance of Proper Flux Temperature Control
Temperature control of the flux solution is critical for the proper functioning and optimal output of the galvanizing process. This means that if the temperature of the flux solution is not within the right range, the following may happen:
Effects of Flux Temperature on the Formation of Dross
You do not wish to have an accumulation of dross in the galvanizing kettle to an extent that is beyond reasonable. Skum is the scum formed as a crust at the surface of the molten zinc bath due to oxidation and impurities. An excess of this impurity can negatively affect the properties of the galvanized coatings, and defects may occur.
Another important parameter that affects the dross levels is the fluxing temperature. When the flux enters the zinc bath, if the temperature of the flux is too high, it will result in excessive drooling and poor quality of the bath surface. Temperature control of the heating system involved in proper flux heating is of paramount importance.
Optimize Flux Liquefaction
The flux must be molten enough to yield the tin bath before getting into the galvanizing bath. It is observed that partially solid flux particles contribute to the formation of dross and an uneven protective layer. In order to achieve complete liquefaction, the ideal flux temperature range must be maintained. This enables the liquid flux to float on the zinc surface and facilitate the removal of oxidation, as well as providing a base for the formation of the desired galvanized layer.
Consistent galvanized coating quality
This means the temperature of the flux is fluctuating, which causes different production runs to have different coating quality and thickness. Temperature control enhances repeatability.
Therefore, the right flux viscosity and reactivity are achieved through adequate heating. This way, it does not allow for the consumption of zinc in excess while at the same time removing oxidation for a clean, uncontaminated galvanized surface every time.
Maximize Flux Efficiency and Lifetime
Exposing the flux to high temperatures results in early failure and loss of flux. Correct temperature control gets the maximum usable life out of the flux before it is required again.
Efficient heating also helps to decrease the overall flux usage rate. This way, you maximize the use of your flux supply and do not compromise the quality of your galvanized coating or your production rate.
Common Flux Heating System Designs
Indirect heating systems
One such design is an indirect heating system. In this design, the flux is heated through the use of a heat exchanger or a jacketed pipe that is passed through. While the heat source, such as steam or a thermal fluid, circulates through the jacket, the flux flows through the pipe. This one is rather indirect, but the temperature is well regulated and the risk of burning is low.
Direct-fired heating
Another type is direct-fired heating. Here, the flux tank has submerged burners or an external firebox in which the flux is heated directly. While this is efficient, it is necessary to ensure that the design is such that overheating occurs in localized regions and the flux degrades. Stirring is useful for heat distribution.
Electric Heating
For small production facilities, electric immersion heaters placed in the flux tank can be effective. The heaters are directly immersed in the flux bath. The temperature setting is easily controllable through the panels installed. Nonetheless, electric systems are known for having relatively higher operating costs than fuel-fired systems.
Combined Designs
While some plants employ a dual heating system where the principal flux holding tank is heated differently than the circulation tanks, For example, the bulk flux may be indirectly heated, while the process tank size may be heated through electric immersion heaters. The optimal solution varies in every facility, depending on the demands and limitations of the particular situation.
It is clear that in any type of heating system selected, insulation, controls, and safety are very important. The ideal flux temperature range is critical to realizing successful hot-dip galvanizing services, specifically in terms of coating adhesion and coverage.
Benefits of a Well-Designed Flux Heating System
Consistent Flux Temperature
Proper energy management of the Flux Heating System in a Hot Dip Galvanizing plant provides adequate heat to maintain the flux solution at its required temperature range. This is important for the proper cleaning of the metal surface to ensure that it is free from oxides and other contaminants in preparation for the galvanizing process.
This is because fluxes require correct temperatures in order to melt and spread evenly over the steel surface to ensure that a proper coat of the galvanized layer is formed. With good heat regulation, this ensures that there is consistent flux deposition.
Improved Energy Efficiency
High-efficiency flux heating solutions provide optimal energy management as heat loss is kept to a minimum. It does this through integrated advanced insulation, heat recovery systems, and intelligent controls, which reduce costs over time.
This lowers your expenses on power while helping you meet your sustainability objectives, making it an excellent thing for your business.
Longer Service Life
Materials that are used in quality heating system components are made to last due to the testing conditions in a galvanizing plant. With the right choice of materials, ranging from corrosion-resistant materials to strong building construction, it is possible to achieve many years of operation with relatively minimal maintenance.
This translates into lower lifecycle costs and less disruption to your production line due to premature failure of key equipment or extended downtime.
Streamlined Operations
Centralized controls, automatic acquisition, and convenient terminal interfaces facilitate the control of the flux heating process. It is very simple and effective to control the parameters to ensure they are at the desired levels, identify any problems, and correct them from a single control desk.
This integrated approach increases efficiency and coordinates activities to avoid mistakes that may affect the coating’s quality or the safety of employees. Through process management, your system in your galvanizing line operates optimally without issues.
Why Choose Arvind Anticor’s Hot-Dip Galvanizing Plants?
Arvind Anticor is among the suppliers of flux heating systems for hot dip galvanizing plants. Our systems are custom-built to ensure that the client gets a reliable and efficient method of heat delivery. Several flux heating systems have been designed over the years of experience that we have had in the industry to enhance the efficiency and productivity of hot dip galvanizing plants.
Our flux heating systems are used to regulate the temperature of the flux solution required for the operation of the galvanizing process. When constructing our systems, we incorporate the best materials and technologies in order to guarantee their functionality and longevity. It also ensures that our systems are easy to maintain and operate, thereby lowering the maintenance costs of the galvanizing process.
Conclusion
A flux heater is an absolute necessity for hot dip galvanizing plants and is used to heat the flux to the required temperature. The system is also tasked with the responsibility of keeping the flux solution at the right temperature so that the galvanizing process runs smoothly. Prospective hot dip galvanizing plants can enhance their efficiency and productivity, as well as diminish maintenance expenses, by using a proficient flux heating system, including the products provided by Arvind Anticor.
Contact us today to learn more about our flux heating systems and how they can benefit your hot dip galvanizing plant.
Let’s Connect
Contact Us
We are live 24/7 and reply within 48 hours.
Get in Touch
-
-
-
Address
Survey No.584/1+2 – C,Nr. Akshar Industrial Estate Mahemdabad Highway Road,Vatva Ahmedabad-382445, Gujarat, India.