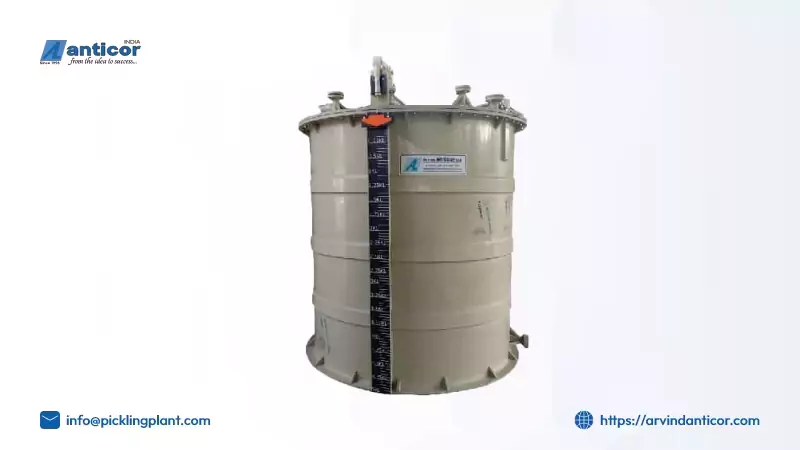
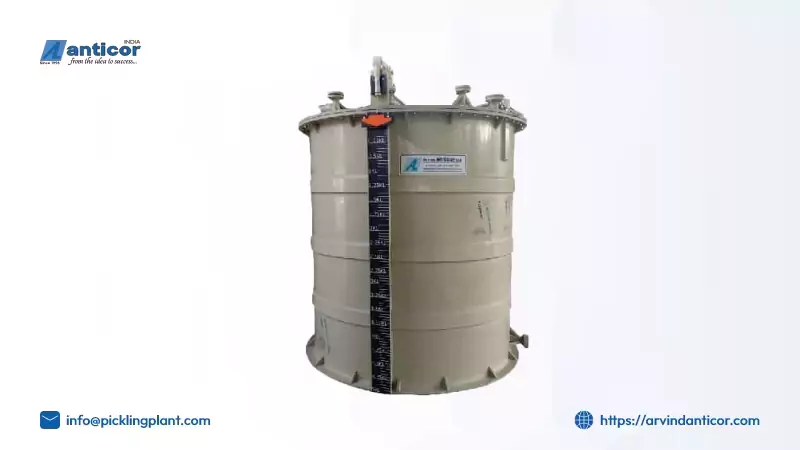
You know how crucial it is to keep tabs on the levels in your chemical storage tanks. If they run too low, production can grind to a halt. Too high and you risk dangerous spills or equipment damage. Measuring chemical tank levels accurately and consistently is a must for safe and efficient operations.
In this blog post, we will explore five accurate ways to measure the levels of chemical storage tanks. These methods have been proven effective in various industries and applications. By understanding these techniques, you can make informed decisions about selecting the most suitable method for your specific needs
1. Reverse Float Level Gauge
It is a simple and safe way to measure chemical storage tank levels outside the tank wall. It is widely used in the chemical industry to monitor the liquid level in storage tanks. And it works for chemical storage tanks types.
How Reverse Float Level Gauge Works
It works best to measure chemical tank levels. However, this can vary based on factors such as gauge design, installation, and maintenance. As the liquid level rises, the float rises with it, and the cable is pulled through a pulley system, indicating the level of the liquid outside the tank. The lower the indicator, the fuller the tank.
As the tank is filled, the chemical lifts the float inside the storage tank, and the level indicator on the outside is lowered. As a reverse float level gauge indicates how full the chemical storage tank is, it eliminates the need for direct contact with the chemicals, enhancing safety during measurement.
Advantages of Reverse Float Level Gauge:
- A simple and safe method for measuring chemical tank level gauge from outside the tank wall.
- Eliminates the need for direct contact with the chemicals, enhancing safety during measurement.
- Provides accurate and reliable measurements, allowing operators to monitor the liquid level in real-time.
- Easy to install and maintain.Suitable for a wide range of chemical storage tanks.
They are a reliable and safe method for measuring the levels of chemical storage tanks. It provides accurate and real-time information about the number of chemicals stored, allowing for effective inventory management and process control. Its simplicity, safety, and accuracy make it a popular choice in the chemical industry.
2. Calibration and Sensor Technology
It plays a crucial role in getting accurate the measure the levels of Chemical Storage tanks. By utilizing advanced sensor systems and calibration methods, operators can ensure precise and reliable measurements for effective inventory management. The chemical tank level gauge techniques involve the use of various sensors and instruments to monitor.
The apparatus includes sensors that are placed within the tank to sense the liquid levels along with metering devices for measuring the amount of liquid. Combined with these essential techniques, ensure accurate measurement of chemical storage tank levels, contributing to safe and optimal operations.
3. Pressure Sensors
To measure chemical tank levels, the pressure sensors technique works best. However, it might vary based on factors such as gauge design, installation, and maintenance. Accurately measuring the levels of chemicals in storage tanks, pressure sensors are a tried-and-true method. Pressure sensors, also known as pressure transducers, measure the hydrostatic pressure of the liquid in the tank to determine the level.
How Pressure Sensors Work
It contains a diaphragm or bourdon tube that flexes under the pressure of the liquid in the tank. This flexing actuates an electrical signal that corresponds to the pressure reading.
The pressure reading is then converted into a level measurement based on the density of the chemical in the tank.
- It can be installed on the tank at the top (for vapour space measurement). And bottom (for interface level measurement), or at various sites (for level profiling).
- They must be calibrated for the individual chemical and require a still, non-agitated liquid to perform effectively.
- They are extremely accurate, but they are more expensive than other solutions.
- They are ideally suited for high-value or dangerous substances when precision is required.
Overall, precise and dependable chemical tank level gauge measurement safety and accuracy are priorities. Pressure sensors are a proven and trustworthy choice.
With the best options choose one of the best chemical storage tank manufacturers who can provide a comprehensive view of tank levels. Also, ensure you have the data you need to monitor your chemical storage operation properly.
4. Radar Gauges
It uses high-frequency radio waves to measure the levels of Chemical Storage tanks. This non-contact method can measure tank levels through obstacles like tank roofs or access hatches. Radar gages transmit radio frequency pulses toward the surface of the chemical in the tank.
When the signal reaches the surface, it bounces back to the gage. By measuring the time it takes for the signal to return, the gauge can calculate the distance to the surface.
Also, determine the level in the tank. While radar gaging does have a higher upfront cost, its precision, low maintenance, and suitability for hazardous environments. That is what makes it a top choice for many chemical storage applications. Keeping close tabs on your tanks’ full will ensure an efficient chemical tank level gauge and a safer work environment.
5. Ultrasonic Gauge
One of the most accurate ways to measure the levels of Chemical Storage tanks is using an ultrasonic gauge. This method uses high-frequency sound waves to detect the level of liquid in the tank.
An ultrasonic gauge has a transmitter that emits ultrasonic pulses, which travel down to the surface of the liquid in the tank. The sound waves then reflect off the liquid surface and travel back up to the receiver. The gauge can calculate the distance to the liquid surface and determine the tank level by measuring the time it takes for the signal to return.
Ultrasonic gages are non-contact, so they never come into direct contact with the chemical being measured, making them ideal for hazardous or corrosive chemicals. Ultrasonic gages can measure a wide range of chemicals since they rely on the reflection of sound waves and not the chemical properties.
The main downside of ultrasonic gages is that they typically require still, turbulence-free liquid surfaces to get an accurate reading. Agitation in the tank can disrupt the sound waves and impair measurement.
If your chemical storage tanks contain relatively still liquids and you need a highly accurate, non-contact measuring method, an ultrasonic gauge is an excellent choice. With no moving parts, they tend to require little maintenance and can provide years of reliable level detection.
For the most precise measurements, choose a gauge with multiple transmitters and receivers around the tank.
Final Words,
So there you have it, the top five ways to accurately measure chemical tank levels. While manual methods like the tape measure or sight glass can work in a pinch, for the most precise readings, you’ll want to invest in a reverse float level gauge is the best way for chemical storage tanks types and gives you an instant digital readout of your tank levels so you know when it’s time for a refill.
To ensure the utmost safety and efficiency in your chemical storage, it is recommended to consult with Arvind Anticor, a trusted provider of chemical storage tank manufacturers.
Request a free consultation today to discuss your specific needs and explore the best solutions for your chemical storage requirements. Keep those tanks filled, keep operations running smoothly, and keep your facility compliant. You’ll be glad you did!
Let’s Connect
Contact Us
We are live 24/7 and reply within 48 hours.
Get in Touch
-
-
-
Address
Survey No.584/1+2 – C,Nr. Akshar Industrial Estate Mahemdabad Highway Road,Vatva Ahmedabad-382445, Gujarat, India.